Low pressure casting process characteristics and development and application
Release time:2023-11-07
Low pressure casting process characteristics and development and application
The prototype of low pressure casting can be traced back to the beginning of the last century. The application for aluminum alloys was made in France in 1917 and in Germany in 1924, but did not form large-scale industrial production. Production for commercial purposes began in 1945 after World War II, when Mr. Lewis of the United Kingdom founded the Arumascu Company, which began to produce rainwater pipes, beer containers, etc. In the 1950s, Austria and Germany began to produce cylinder heads. In 1958, the United States Zenella Lumercus used a large number of aluminum alloy castings on the engine parts of small cars (cylinder heads, boxes, gear boxes), and adopted the low-pressure casting method. This is an indispensable boost for the low pressure casting method that is still widely used today, especially in the automotive industry around the world. Low pressure casting method was introduced into China around 1957, but it really attracted the attention of the industry, began to carry out a variety of research, the introduction of equipment from around 1960. However, this epoch-making process, which broke previous common sense, has almost no riser and is completely different from the gravity gold casting technology that has been established as a "technology", so the industry's response is relatively cold.
Development history:
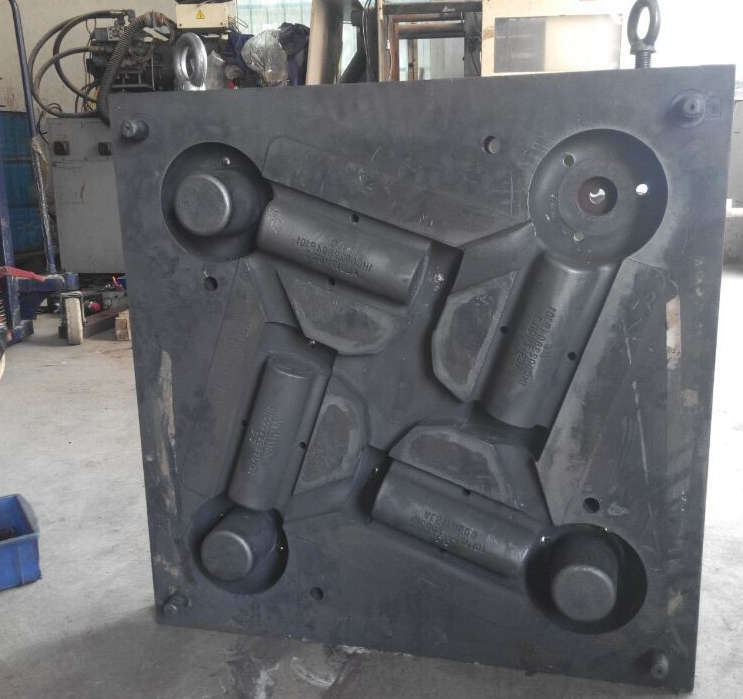
In this situation, the production of air cooled cylinder heads for light vehicles in 1961 became the beginning of the practical application of low pressure casting method in China. The future development is very rapid, after overcoming a number of technical problems, the use of low pressure casting method has the advantages of high material utilization, easy to realize the automation of the injection, and gradually established the strong position of the main casting method of light alloy castings in the center of automotive parts. In the production of aluminum alloy castings, low-pressure casting products have accounted for about 50%, and is known for its huge production and excellent quality. Products expanded to automotive related parts, such as cylinder head, cylinder block, brake drum, clutch cover, hub, intake manifold and so on. Especially after 1970, a large number of applications in the wheel hub, and with the requirements of lightweight and improved performance, in the past, under the strict requirements of complex internal quality and mechanical properties, the use of cylinder head and cylinder block has gradually increased.
The basic principle:
Air pressure or inert gas pressure 0.01~0.05Mpa higher than atmospheric pressure is applied to the liquid surface of the closed holding furnace. The liquid rises through the feed pipe (riser pipe) immersed in the liquid soup and is pressed into the upper mold connected to the furnace. The soup is filled slowly from the lower part of the cavity and held under pressure for a period of time before solidifying. Solidification is transferred from the upper part of the product to the direction of the gate, and the moment when the gate is partially solidified is the time when the pressure ends. Therefore, the perfect casting is obtained by virtue of the directional solidification of the gate and the effect of the riser pressure from the gate. Finally, when the casting is cooled below the solid phase temperature, the product can be removed from the mold.
Process principle:
Figure 1-38a shows the low-pressure casting device. The dry compressed air is slowly injected into the crucible furnace, and the metal liquid is filled with the cavity along the liquid riser and pouring system from bottom to top under the action of gas pressure, and the casting is opened and the casting is taken out.
Technical features:
(1) The pressure and speed of pouring can be adjusted, so it can be applied to a variety of different molds (such as metal molds, sand molds, etc.), casting various alloys and castings of various sizes.
(2) The use of bottom injection type filling, metal liquid filling is stable, no splash phenomenon, can avoid gas involvement and erosion of the mold wall and core, improve the qualified rate of casting.
(3) The casting crystallizes under pressure, the casting structure is dense, the outline is clear, the surface is smooth, and the mechanical properties are high, which is especially advantageous for the casting of large thin-walled parts.
(4) Eliminating the feeding riser, the metal utilization rate is increased to 90 ~ 98%.
(5) Low labor intensity, good working conditions, simple equipment, easy to achieve mechanization and automation. [1]
Advantages and disadvantages (relative to gravity gold casting)
Merits and demerits
Advantages:
Because there is no riser and runner, the gate is smaller, so the material cost and processing time can be greatly reduced.
2) Get the perfect casting.
Easy to form directional solidification, less internal defects.
3) Less gas and debris involvement.
The pressure rate can be changed, and the liquid is filled by laminar flow.
4) Sand core can be used.
5) Easy to achieve automation, can be multiple operations, multi-process operations.
6) It is not affected by the operator's proficiency.
7) Wide range of materials.
Table 5.1 Material utilization rate of each casting method
Process method |
Gravity gold casting |
High pressure casting |
Low pressure casting |
Material utilization rate (%) |
45~55 |
50~60 |
85~95 |
Cons:
1) The freedom of the gate scheme is small, thus limiting the product.
(Gate location, quantity restrictions, product internal wall thickness changes, etc.)
2) Long casting cycle and poor productivity.
In order to maintain directional solidification and liquid flow, mold temperature is high and solidification speed is slow.
3) The structure near the gate is thick, and the mechanical properties of the lower surface are not high.
4) In order to ensure the shape and position of the gate, comprehensive and strict management (temperature, pressure, etc.) is required.