Six kinds of secondary processing for aluminum alloy die casting parts
Release time:2024-04-15
Six kinds of secondary processing for casting-china.com' target='_blank'>aluminum alloy die casting parts
We will discuss some of the other processes that may occur after the casting is removed from the mold. These processes are called secondary operations or post-pouring.
Why do some die castings require secondary processing?
The process of die-casting aluminum parts is known for its excellent dimensional accuracy and smooth, even surface finish. When taken out of the mold, many die cast parts are already very close to the final desired condition and only need some flash trimming. However, some die casting products require additional handling. This happens when the mold is unable to efficiently provide certain physical features, such as holes, threads, or bottom cuts. Secondary operations may also be required to achieve other product properties. For example, some applications may require surface properties that aluminum cannot provide on its own, or require surfaces other than the smooth surfaces offered by die casting.
Six kinds of aluminum die casting parts common secondary processing
The best known and most commonly used die casting secondary processes are finishing, machining, dipping, polishing, tumbling and surface treatment. With thoughtful mold design and alloy selection, it is often possible to limit the time and money spent on these post-casting operations. But sometimes they are unavoidable, especially if you want to get unique characteristics that aluminum die casting itself can't provide.
No. 1: Finishing
Pruning is done for a variety of reasons, but the most common reason is to address flash memory defects. Due to the high pressure involved in the die casting process, excess material can form around the parting line of the casting. It ends up looking like a "seam" of two (or more) die parts. Especially for consumer goods, you have to remove excess material by trimming, which requires hand tools or special trimming molds. In addition to hair removal.In addition to the edge, the manufacturer also needs to trim other parts of the mold filled with molten metal. These include sprue, vent, overflow and runner, depending on the mold design. While robust mold design minimizes the number and complexity of finishing operations, basic finishing is often unavoidable.
No. 2: Machining (also known as CNC machining)
Die casting is a precision process, so die casting products generally do not require special machining to meet dimensional tolerances. Conversely, when creating features that cannot be achieved by a die casting process, it is often necessary to machine the die cast part. Techniques involving the use of various cutting tools and machinery to remove material from workpieces. It is often used to achieve precise dimensions, create complex shapes, improve surface finish, or add specific functionality to components. Pore and snail
Grain and bottom cut are examples of shapes that are often very difficult and inefficient to cast. But by using a secondary processing process, you can create them. Computer numerical control (CNC) machines allow you to quickly perform any necessary machining operations. They also help ensure that products meet quality tolerances more consistently.
No. 3: Polishing
These techniques are used to improve surface finish and enhance the appearance of die castings. It also removes any surface defects and provides a smooth, shiny or reflective surface. It involves the use of abrasive materials such as sandpaper or polish to smooth the surface of the part by using progressively finer abrasives to achieve a high-quality finish.
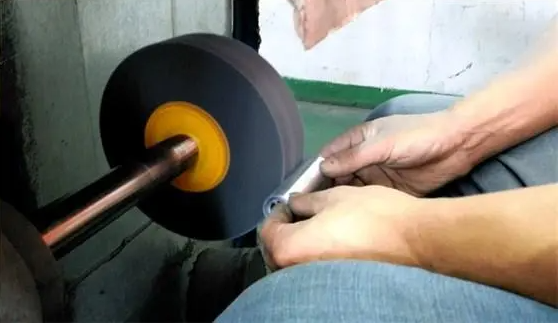
No. 4: Tumbling
The process of placing a die cast in a rotating barrel and rolling it with a grinding medium, compound or polish. It helps improve zero
The overall appearance, cleanliness and function of the piece. It removes sharp edges, burrs and contaminants, resulting in smoother edges. The grinding is OK
To create a more uniform surface finish and prepare the part for subsequent coating, painting or assembly processes.
No. 5: Dipping
Some porosity is inevitable in any casting process, but some applications (such as pressurizing equipment) may require the casting to be completely leak-proof. Impregnation uses a vacuum and specially formulated organic resin to remove air from any open pores (voids) on the surface of the part, then fills and seals the pores. Impregnation can be used on castings to reduce water retention and internal corrosion. It also helps to inhibit fungal growth and seal leaks to ensure pressure tightness. This process can be expensive, but costs can be minimized by pressure testing all castings and applying the process only to castings that do not meet specifications.
No. 6: surface treatment
Products can be surface treated in a variety of ways to enhance their physical and chemical properties after other processes have been completed. Mechanical surface finishing operations, such as polishing, sanding or deburring, can help improve the surface finish of a part. On the other hand, sandblasting techniques (such as shot blasting) can be used to roughen smooth surfaces if desired. Aluminum castings can also be painted, powder coated or anodized to enhance physical wear resistance, prevent corrosion and improve appearance. However, it is crucial to conduct thorough research before implementing any of these coatings, their feasibility depends on your application, and the decision is not as simple as an aluminum extrusion.
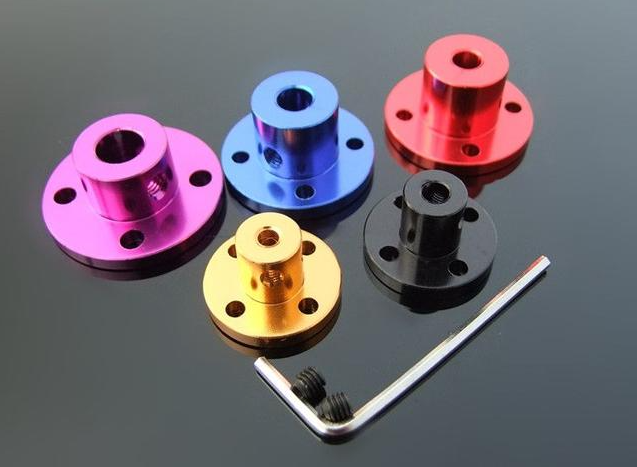