One minute takes you to know the types of casting
Release time:2023-09-26
One minute takes you to know the types of casting
Ordinary sand casting
The use of sand as a casting material, also known as sand casting, sand casting, including wet sand, dry sand and chemical hardening sand 3 categories, but not all sand can be used for casting. The benefit is that the cost is lower because the sand used in the mold can be reused; The disadvantage is that the casting process is time-consuming, the casting itself cannot be reused, and the finished product must be destroyed before it can be obtained.
Sand (core) casting method: wet sand type, resin self-hardening sand type, water glass sand type, dry and surface dry type, solid casting, negative pressure modeling.
Sand core manufacturing method: It is selected according to the size, shape, production batch and specific production conditions of sand core. In production, it can be divided into manual core making and machine core making in general.
Special casting
According to the molding materials, it can be divided into two categories: special casting with natural mineral sand and stone as the main molding materials (such as investment casting, mud casting, shell casting, negative pressure casting, solid casting, ceramic casting, etc.) and special casting with metal as the main casting materials (such as metal casting, pressure casting, continuous casting, low pressure casting, centrifugal casting, etc.).
1. Gravity casting
Gravity casting refers to the process of injecting metal liquid into the mold under the action of Earth gravity, also known as casting. Generalized gravity casting includes sand casting, metal casting, investment casting, mud casting, etc. Narrow gravity casting refers to metal mold casting.
2. Pressure casting
Pressure casting refers to the process in which liquid metal is injected into the mold under the action of other external forces (excluding gravity). The generalized pressure casting includes pressure casting and vacuum casting of die casting machine, low pressure casting, centrifugal casting [2] and so on. Narrow pressure casting refers to the metal type pressure casting of die casting machine, referred to as die casting. These casting processes are the most commonly used in non-ferrous metal casting and are also the lowest in relative price.
3. Sand casting
Sand mold casting is a traditional casting process that uses sand as the main molding material to make the mold.
Gravity casting is generally used for sand mold, and low pressure casting, centrifugal casting and other processes can also be used when there are special requirements. The adaptability of sand casting is very wide, small pieces, large pieces, simple pieces, complex pieces, single pieces, large quantities can be used. The mold used for sand casting used to be made of wood, commonly known as wood mold. The disadvantages of wood mold are easy to deform and damage; In addition to the sand castings produced by a single piece, aluminum alloy molds or resin molds with high dimensional accuracy and long service life can be used. Although the price has increased, it is still much cheaper than the mold used for metal casting, and the price advantage is particularly prominent in small batch and large production. In addition, sand has a higher refractoriness than metal, so materials with higher melting points such as copper alloys and ferrous metals are also used in this process. However, sand casting also has some shortcomings: because each sand casting can only be cast once, the cast is damaged after obtaining the casting, and it must be re-shaped, so the production efficiency of sand casting is low; And because the overall nature of sand is soft and porous, the dimensional accuracy of sand casting is low, and the surface is rough.
4. Special casting method
Metal mold casting is a modern technology of making hollow mold with heat-resistant alloy steel for casting. The metal mold can be cast by gravity or by pressure casting. The metal mold can be used repeatedly, and every time the metal liquid is poured, a casting is obtained, which has a long life and high production efficiency. Metal castings not only have good dimensional accuracy and smooth surface, but also in the case of pouring the same metal liquid, the strength of the casting is higher than that of the sand type, and it is less likely to be damaged. Therefore, in the mass production of small and medium castings of non-ferrous metals, as long as the melting point of the casting material is not high, metal casting is generally preferred. However, the metal mold casting also has some shortcomings: because the heat-resistant alloy steel and the processing of the hollow cavity on it are more expensive, the metal mold is expensive, but the overall cost is much cheaper than the die casting mold. For small batch production, the mold cost allocated to each product is obviously too high, and it is generally not acceptable. And because the metal mold is limited by the size of the mold material and the capacity of the cavity processing equipment and casting equipment, it is also helpless for particularly large castings. Therefore, in small batch and large production, metal mold casting is rarely used. In addition, although the metal mold uses heat-resistant alloy steel, the heat resistance is still limited, generally used for aluminum alloy, zinc alloy, magnesium alloy casting, in copper alloy casting has been less applied, and for black metal casting is even less.
Die casting is a metal type pressure casting on a die casting machine, which is the casting process with the highest production efficiency at present.
Die casting machines are divided into hot chamber die casting machines and cold chamber die casting machines. Hot chamber die casting machine has high degree of automation, less material loss and higher production efficiency than cold chamber die casting machine, but limited by the heat resistance of the machine, it can only be used for the production of low melting point materials such as zinc alloy and magnesium alloy. The aluminum alloy die-casting parts widely used today can only be produced on cold chamber die-casting machines due to their high melting point. The main feature of die casting is that liquid metal fills the cavity under high pressure and high speed, and forms and solidifies under high pressure. The shortcomings of die casting parts are: Because the liquid metal in the process of filling the cavity at high pressure and high speed, the air in the cavity is inevitably wrapped in the inside of the casting, forming subskin pores, so the aluminum alloy die casting is not suitable for heat treatment, and the zinc alloy die casting is not suitable for surface spraying (but can be painted). Otherwise, the internal pores of the casting will expand when heated by the above treatment, resulting in deformation or bubbling of the casting. In addition, the mechanical cutting allowance of die casting parts should also be smaller, generally about 0.5mm, which can reduce the weight of the casting, reduce the amount of cutting to reduce costs, and avoid penetrating the dense layer on the surface, exposing the subcutaneous pores, resulting in the scrap of the workpiece.
6. Investment casting
Lost wax casting is now known as investment precision casting, is a less cutting or no cutting casting process, is an excellent process technology in the casting industry, its application is very wide. It is not only suitable for the casting of various types and various alloys, but also the dimensional accuracy and surface quality of the castings produced are higher than other casting methods, and even the complex, high temperature resistant, and not easy to process castings that are difficult to cast by other casting methods can be cast by investment precision casting.
7. Vanishing mold casting
EPC or LFC is a casting method in which foam is made into a solid mold with the same structure and size as the part, which is soaked with refractory adhesive paint, dried and molded in dry sand, vibrated and compacting, and then poured into metal liquid to make the shape disappear by heating and vaporized, so as to obtain metal parts with the same shape. Lost mold casting is a new technology with near zero margin and precise forming, which does not require closed box to take the mold, and uses binder-free dry sand modeling to reduce pollution, which is considered to be the most likely process technology to achieve green casting in the 21st century.
8. Fine crystal casting
The principle of fine crystal casting technology or process (FGCP) is to strengthen the nucleation mechanism of the alloy by controlling the ordinary investment casting process, make the alloy form a large number of crystalline cores during the casting process, and prevent the grain growth, so as to obtain uniform, fine, isotropic equiaaxial crystal castings with an average grain size of less than 1.6mm. The grain size of the typical fine crystal castings is ASTM0~2. Fine crystal casting not only makes the casting grain fine, but also makes the primary carbide and strengthening phase in the superalloy. The size is reduced, the shape is improved. Therefore, the outstanding advantage of fine crystal casting is to greatly improve the low-cycle fatigue life of castings at medium and low temperature (≤760℃), and significantly reduce the dispersion of mechanical property data of castings, so as to improve the design tolerance of cast parts. At the same time, the technology also improves the tensile and durable properties of the castings to a certain extent, and makes the castings have good heat treatment properties.
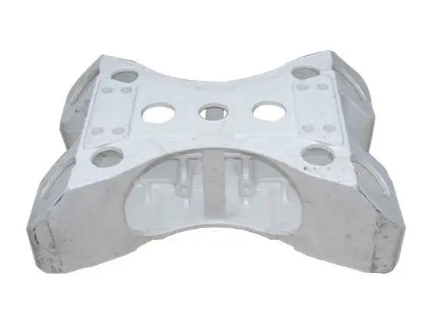